Chatbots Are Trying to Figure Out Where Your Shipments Are
Logistics companies are looking at generative AI for use in customer support, but the technology carries risks in high-value, industrial supply chains
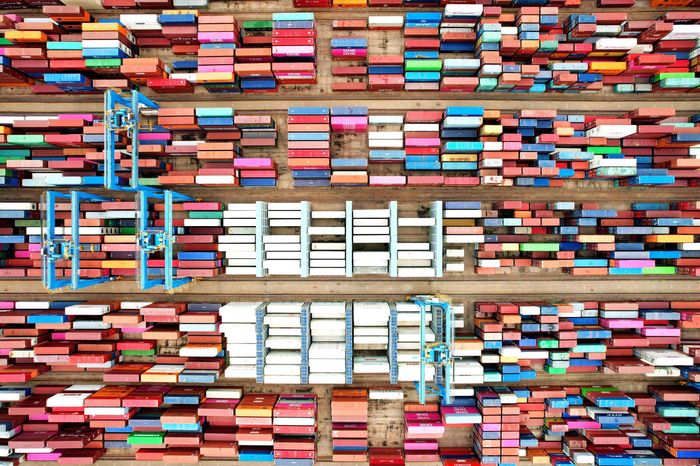
Logistics companies are eyeing the potential of artificial intelligence, particularly generative AI tools like ChatGPT, to revolutionize their operations. However, they’re treading carefully, especially when it comes to chatbots, which are becoming commonplace in the consumer sector.
Why the caution? The logistics industry deals with the movement of goods worth millions, and the last thing they want is to frustrate their customers. Companies like RXO, XPO, Phlo Systems, and DFDS are exploring how this AI can automate tasks in their customer service departments, such as tracking shipments and booking loads.
Generative AI, like OpenAI’s ChatGPT, can sift through vast amounts of data, recognize patterns, and answer questions in a human-like manner. This capability has already been harnessed in other sectors. Law firms use AI for legal research and document drafting, while retailers use it to analyze customer queries. Even travel and grocery sectors have jumped on the bandwagon, with companies like Expedia and Instacart using bots to assist customers.
For logistics, the immediate application of generative AI seems to be in customer support. The technology can comprehend questions in everyday language and provide comprehensive answers swiftly. This could enhance the customer experience, offering precise answers quickly, unlike traditional chatbots with their preset responses or human agents who might need more time.
However, there are challenges. Generative AI’s effectiveness hinges on the quality of its training data. Sometimes, it might get answers wrong. There are also valid concerns about using sensitive company or customer data to train these systems. Some companies have even prohibited their employees from using tools like ChatGPT due to these concerns.
The stakes are undeniably high in logistics. The industry deals with complex, proprietary data related to moving vast quantities of goods via various transportation modes. As such, while the allure of AI is strong, the logistics sector is approaching it with a mix of optimism and caution.