How Manufacturers Can Optimize their Supply Chain Workforce
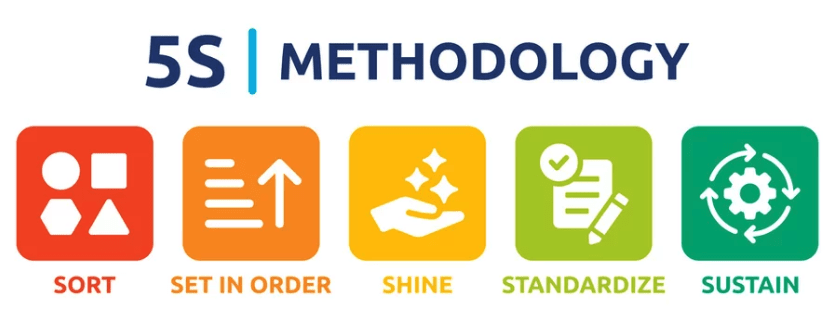
Adopting a 5S workplace organization strategy can be the key to a successful post-COVID workforce. By implementing these policies, manufacturers will be able to optimize their supply chains and workforces in a way that will allow them to overcome the challenges they have faced since the COVID-19 pandemic.
The manufacturing sector has faced several enormous challenges since the pandemic. From supply chain disruptions to labor shortages that are still leaving many companies understaffed, manufacturers are struggling, causing a ripple effect that has left no link of the manufacturing process unaffected.
But by adopting strategies to optimize the supply chain and workforce efficiency, manufacturers can stand tall in the face of these challenges and come out the other side even stronger.
Workplaces that hope to be efficient in the post-COVID environment should strive to adopt what is known as a lean management strategy. Lean management was pioneered by Toyota and involves eliminating waste at every step of the supply chain—including the workforce.
Not only does eliminating waste help reduce the pressure manufacturers face due to current social and economic conditions, but it also makes the process more efficient and saves companies money in the long term.
One easy way for companies to minimize waste is to emphasize quality control throughout the entire manufacturing process. Too often, manufacturers only perform a quality control check at the end of production, meaning entire defective product lines—and the labor used to produce them—go to waste. By investing in quality control in the earlier stages of manufacturing, companies can catch rejected products before too much is invested in them in terms of labor and raw materials.
Another important strategy for manufacturers to adopt is called Hoisin Kanri. This Japanese business strategy, which was also developed by Toyota, involves aligning a company under a unified, “true north” vision across departments and teams.
Since Hoisin Kanri entails the creation of a company-wide strategy, dramatic changes can be implemented relatively quickly throughout the entire organization.
Adopting a 5S workplace organization strategy can also be the key to a successful post-COVID workforce. In this strategy, business leaders work to identify value-added and non-value-added activities in the workplace and devise practical solutions to help implement lean logistics principles.
Each “S” in the 5S organization strategy represents a different Japanese principle whose application helps make the supply chain more efficient.
- Sort (Seiri): By eliminating unnecessary items and materials from the supply chain, production employees can easily access the materials they need to complete their jobs. Employers should also strive to remove as many physical and non-physical barriers as possible that prevent their employees from reaching maximum productivity.
- Set in Order (Seiton): The organizational structure of the business is key to its efficiency. An ineffectively organized business wastes time between two links in the supply chain. If each part of the supply chain—from the warehouse to the front office—is precisely and expertly organized, businesses can much more easily navigate the complexities and unique challenges of their supply chain.
- Shine (Seiso): Studies have long discussed that clean workspaces lead to better efficiency in the workplace. However, cleaning should go far beyond the type of cosmetic cleaning used to keep up appearances. Thorough inspections and cleanings of resources and equipment allow businesses to identify any inefficiencies early in the process and respond to them with any potentially necessary repairs.
- Standardize (Seiketsu): To effectively manage these three steps, organizations must implement standardized policies and procedures for their enforcement. This standardization ensures consistency in initiatives across the entire organization.
- Sustain (Shitsuke): Finally, after developing the procedures and standardizing them in a way that can be efficiently implemented, workers must be trained and educated in these policies to ensure they know how to effectively implement them in their day-to-day operations.
By implementing these policies, manufacturers will be able to optimize their supply chains and workforces in a way that will allow them to overcome the challenges they have faced since the COVID-19 pandemic.
Although there is no one-size-fits-all solution to every business’s struggles, these policies can help improve performance and boost the overall bottom line.